Foxboro Pressure Transmitter Installation
Browse and Read Foxboro Installation Manual Pneumatic Pressure Transmitter Foxboro Installation Manual Pneumatic Pressure Transmitter It's coming again, the new. Foxboro Installation Manual Pneumatic Pressure Transmitter Foxboro installation manual pneumatic pressure transmitter, download and read foxboro installation manual.
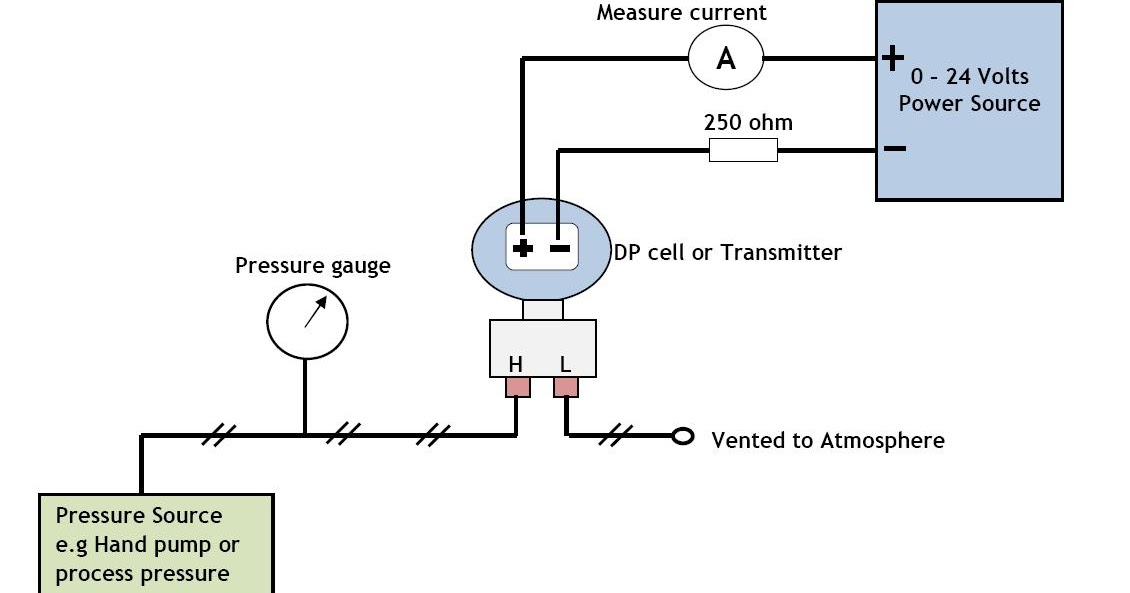
Gauge Pressure Transmitter IGP20 Manufactured by The I/A Series® Model IGP20 is an intelligent, two-wire gauge pressure transmitter that provides precise, reliable, measurement of gauge pressure, and transmits a 4 to 20 mA output signal with HART, FoxCom™, and FOUNDATION fieldbus, communication protocols, software selectable, for remote configuration and monitoring. Long-term stability with drift is less than 0.05% of URL per year for 5-years. Key Benefits. Simple, elegant sensor packaging uses very few parts to achieve exceptionally high reliability. Liquid Crystal Display (LCD) digital indicator with on-board pushbutton configuration and calibration. NEMA 4X and IEC IP66 durable epoxy-coated aluminum, or 316 ss housings.
Co-Ni-Cr, 316L ss, and Nickel alloy (equivalent to Hastelloy®(1)) sensor materials for all transmitters. Can be provided with numerous configurations of direct connect or remote mount seals. Choice of Mounting Styles: IGP20 for compact light weight and direct-to-process mounting (bracket optionally available. Rugged & Dependable: Field-proven silicon strain gauge technology and corrosion-resistant epoxy finish. Superior Performance: High accuracy to 0.05% of calibrated span in the digital linear mode, and 0.06% of calibrated span in the 4 to 20 mA linear mode. Rugged & Dependable: Ambient temperature effects to 0.02% URL per 55 C (100 F) change of normal operating conditions.
Best in the industry - 5 year warranty FEATURES. Silicon strain gauge sensors successfully field proven in many thousands of installations.
Simple, elegant sensor packaging with very few parts; achieves exceptionally high reliability. Aluminum housing has durable, corrosion resistant epoxy finish; 316 ss housing also available; both meet the ratings of NEMA 4X and IEC IP66. Remote configuration or locally via the optional LCD Indicator. Can be provided with numerous configurations of direct connect or remote mount seals. HART protocol allows multidrop topology.
SIL2-Certified transmitter offered as an option. The IAP10 and IGP10 are offered with integral process connections for sanitary, and pulp and paper installations. Also, the IGP10 is offered for high gauge pressure applications to 52, 105, or 210 MPa (7500, 15,000, or 30,000 psi). Sensor wetted parts materials include Co-Ni-Cr, 316L ss, and nickel alloy (equivalent to Hastelloy (1)); additionally, Monel, tantalum, and gold-plated 316L ss sensors are offered for the IAP20/IGP20. CE marked; complies with applicable EMC, ATEX, and PED European Union Directives.
Multi-marking available for ATEX, CSA, and FM intrinsically safe applications. User determines and permanently marks the certification to be applied. Complies with NAMUR NE 21 interference immunity requirement, and NAMUR NE 43 analog output overrange and underrange annunciations. Complies with electromagnetic compatibility requirements of European EMC Directive 2004/108/EC by conforming to following EN and IEC Standards: EN 61326-1, and IEC 61000-4-2 through 61000-4-6. Meet numerous requirements for hazardous locations. Versions available to meet Agency flameproof and zone requirements.
Dual Seal certified by CSA to meet ANSI/ ISA 12. Numerous mounting bracket set options. Many other options and accessories offered.
Standard 5-year warranty. I/A Series® PRESSURE TRANSMITTER FAMILY The I/A Series Electronic Pressure Transmitters are a complete family of d/p Cell®, gauge, absolute, multirange, multivariable, and premium performance transmitters, as well as transmitters with remote or direct connect pressure seals, all using field-proven silicon strain gauge sensors and common topworks. OPTIONAL LCD DIGITAL INDICATOR This is a two-line digital indicator with on-board pushbuttons that displays the measurement with a choice of units. The pushbuttons allow zero and span adjustments, as well as local configuration without the need for a Communicator or PC-based Configurator. MODULAR ELECTRONICS A common HART electronics module is used for all I/A Series HART Pressure Transmitters.
Also, because all configuration and calibration data is stored in the sensor, you can replace a HART module with another HART module without transmitter reconfiguration or recalibration. Furthermore, if your needs change, the transmitter modular design allows easy migration to other standards, including FoxComTM, FOUNDATIONTM fieldbus, and Analog 4 to 20 mA or 1 to 5 V dc. HART Communication Protocol Version (-T Electronics) 4 to 20 mA with HART communications. Allows direct analog connection to common receivers while still providing full digital communications using a Communicator, PC-based Configurator, or optional LCD Indicator. HART Communicators can be upgraded with software to accommodate these transmitters. Also, Invensys will make use of the HART Foundation library of registered DDs (Device Descriptors), and reload a Communicator if the user desires to keep another supplier's DD along with the Foxboro DD. In addition to HART, Invensys also offers transmitters with other protocols as described below.
FOUNDATION Fieldbus Version (-F Electronics) This is a FISCO/FNICO compliant all digital, serial, two-way communication system which interconnects field devices such as transmitters, actuators, and controllers. It is a local area network (LAN) with built-in capability to distribute control across the network. Analog Output Version (-A Electronics) Provides a 4 to 20 mA analog output and includes a standard LCD Indicator to provide transmitter configuration directly from on-board pushbuttons. Analog Output Version (-V Electronics) A low power, low voltage transmitter that draws no more than 3 mA, and transmits a 1 to 5 V dc output signal. As with the -A version, it includes a standard LCD Indicator. Refer to PSS 2A-1C13 D.
HART Intelligent Module Configured for 4 to 20mA Output Measurements and diagnostics are available from the HART Communicator connected to the two-wire loop carrying the 4 to 20 mA measurement signal by using a bidirectional digital signal superimposed on the 4 to 20 mA current signal. Multiple measurements are transmitted digitally, including not only the primary measurement in pressure units, but also the electronics temperature and sensor temperature which can be used to monitor external heat tracing equipment.
Complete transmitter diagnostics are also communicated. Configuration and reranging can be accomplished with the Communicator, PC-based Configurator, or the optional LCD Indicator with pushbuttons.
HIGH PERFORMANCE Both direct-connected and bracket-mounted transmitters utilize microprocessor-based correction to achieve both excellent accuracy and ambient temperature compensation. OPTIONAL SIL2 TRANSMITTERS Modern industrial processes tend to be technically complex and have the potential to inflict serious harm to persons or property during a mishap. The IEC 61508 standard defines safety as “freedom from unacceptable risk.” SIL2 pressure transmitters with HART communication protocol, in conjunction with Triconex Safety Systems, provide integrated solutions for safety and critical control applications.
The integrated solution is certified as interference-free from the 4 to 20 mA loop; this guarantees the integrity of the safety system and the safety of the controlled process. The integrated design allows uninterrupted operation of the safety function, while allowing access to device level information via HART commands.
The solution permits interface of device diagnostics with asset management systems without compromising functional safety. Select Option -S2 for a SIL2-certified HART Transmitter. A copy of the certification is available via Auxiliary Specification (AS) Code CERT-S.
MULTIDROP COMMUNICATIONS Point-to-point or multidrop topologies are permitted. Multidropping is the connection of several transmitters to a single communications line. Communications between the host computer and transmitters takes place digitally with the analog output of the transmitter fixed. Up to fifteen transmitters can be connected on a single twisted pair of wires or over leased telephone lines. CHOOSE MOUNTING CONFIGURATION NEEDED Direct Connected Transmitters (Models IAP10 and IGP10) These transmitters are light weight and easy-to-install. They use 316L ss or nickel alloy (equivalent to Hastelloy®) process connections, and a choice of either 316L ss, Cobalt-Nickel-Chrome, or nickel alloy for the sensing diaphragm. See Direct-Connected Transmitters section.
Bracket-Mounted Transmitters (Models IAP20 and IGP20) These transmitters offer a large selection of corrosion resistant process covers and sensing diaphragm materials. They are suitable for applications requiring low spans, vacuum service, and high overrange pressure. EASE OF INSTALLATION Rotatable Topworks allows transmitter installation in tight places, allows indicator to be positioned in preferred direction, and eases field retrofit. Two Conduit Entrances offer a choice of entry positions for ease of installation and self-draining of condensation regardless of mounting position and topworks rotation. Wiring Guides and Terminations provide ease of wire entry and support, plenty of space to work and store excess wire, and large, rugged screw terminals for easy wire termination. EXCEPTIONAL VALUE The combination of small size, light weight, direct mounting, standard materials,and wide measurement capability with high performance make this an exceptionally cost effective solution for process pressure measurement. DIRECT PROCESS MOUNTING Because of their light weight and external threaded connection, these transmitters can be installed directly on process piping without mounting brackets.However, for unique requirements, an optional bracket is offered and connection can be made to the standard 1/4 NPT internal thread.
WIDE RANGEABILITY Three absolute pressure versions are offered to allow spans from 7 to 21,000 kPa (1 to 3,000 psi), and four gauge pressure versions are offered to allow spans from 7 to 42,000 kPa (1 to 6,000 psi). Refer to IGP20 Transmitter for gauge pressure vacuum service. 316L ss, NICKEL ALLOY, AND Co-Ni-Cr PROCESS WETTED PARTS With process connection of 316L ss or nickel alloy (equivalent to Hastelloy®) and sensor diaphragm available in either 316L ss, nickel alloy, or highly corrosion resistant Co-Ni-Cr, this transmitter is an excellent choice for the vast majority of process pressure measurements. FLAMEPROOF DESIGN The IAP10 and IGP10 flameproof versions are designed to meet Agency flameproof and zone requirements. HIGH GAUGE PRESSURE VERSIONS Three high gauge pressure versions with URLs of 52,105, and 210 MPa (7,500, 15,000, and 30,000 psi)are available in the IGP10 line. SANITARY AND PULP AND PAPER VERSIONS These transmitters are also available with integral process connections for use in sanitary, and pulp and paper installations.
See PSS 2A-1C13 K and PSS 2A-1C13 L, respectively. BRACKET-MOUNTED TRANSMITTER – IAP20 AND IGP20 SENSOR CORROSION PROTECTION Choice of 316L ss, Co-Ni-Cr, nickel alloy (equivalent to Hastelloy®), Monel, Gold-Plated 316L ss, andTantalum materials. High corrosion resistance of CoNi-Cr(TI037-078)means long service life in many difficult applications without the extra cost for exotic materials.Also see TI 37-75b for process applicability with Co-Ni-Cr and other process wetted parts materials. WIDE RANGEABILITY Gauge pressure measurement spans may be as low as 0.12 kPa (0.5 inH O) to as high as 35 MPa (5000 psi) by choosing one of only six sensors, and absolute pressure measurement spans may be as low as 0.87 kPa (3.5 in H 2 O) to as high as 21 MPa (3000 psi) by choosing one of only four sensors.
This provides exceptional measurement range capability with a minimum of versions. HIGH GAUGE PRESSURE VERSIONS Three high gauge pressure versions with URLs of 52,105, and 210 MPa (7,500, 15,000, and 30,000 psi)are available in the IGP10 line. VACUUM SERVICE A lower range limit of -100 kPa (-14.7 psi, -1 bar or kg/cm2 ) means that vacuum measurements are easily handled with the versatile IGP20 Gauge Pressure transmitter. PROCESS CONNECTOR Removable, gasketed process connector (Figure 2)allows a wide range of selections, including 1/4 NPT,1/2 NPT, Rc 1/4, Rc 1/2, and weld neck connections. For highly corrosive chemical processes, a 1/2 NPTpvdf (Kynar) insert, as shown in Figure 3, is installed in the HI-side 316 ss cover and is used as the process connector. In these applications, tantalum is used as the sensor diaphragm material.
EASE OF MOUNTING TWO-VALVE MANIFOLD Optional two-valve manifold to isolate transmitter, and vent pressure, is easily mounted directly to transmitter. FLAMEPROOF DESIGN The transmitters are designed to meet Agency flameproof and zone requirements. FUNCTIONAL SPECIFICATIONS Output Signal and Configuration Output is 4 to 20 mA with digital HART communications. For multidrop applications, the mAsignal is fixed at 4 mA to provide power to the device. Configurable using the HART Communicator, PCbased Configurator, or optional LCD Indicator with on-board pushbuttons.
Electronics and Sensor Temperatures Readable from the Communicator or PC-based Configurator. Measurement is transmitter temperature, at the sensor and the electronic module, not necessarily process temperature. Field Wiring Reversal No transmitter damage. Suppressed Zero and Elevated Zero Suppressed or elevated zero ranges are acceptable as long as the Span and Range Limits are not exceeded (elevated zero applicable to IGP20 only). Zero and Span Adjustments Zero and span adjustments can be initiated using the Communicator, a PC-based Configurator, or the optional LCD with on-board pushbuttons.
Write Protect Jumper Can be positioned to lock out all configurators from making transmitter database changes. This makes transmitter suitable for Safety Shutdown System Applications that require this feature. Supply Voltage Requirements and External Loop Load Limitations Nominal minimum supply voltage is 11.5 V dc. This value can be reduced to 11 V dc by using a plug-in jumper across the test receptacles in the field wiring compartment terminal block as shown in the Physical Specifications section.
. Instruction MI 019-202 February 2012 I/A Series Intelligent Vortex Flowmeter ® Models 84F-T (Styles A and B), 84F-U (Styles A and B), 84W-T, and 84W-U With HART Communication Installation, Operation, and Maintenance. MI 019-202 – February 2012. Contents Figures. Vii Tables. Introduction.1 Overview. 1 Reference Documents.
1 Standard Specifications.2 Electrical Safety Specifications.13 ATEX and IECEx Warnings.14 ATEX Compliance Documents.14 IECEx Compliance Documents.15 Configurable Parameters. MI 019-202 – February 2012 Contents Setting the Write Protect Jumper.
33 Positioning the Housing.34 Electrical Installation. 35 Integrally Mounted Electronics.35 Remotely Mounted Electronics.35 Preparing the Remote Signal Cable.35 Connecting the Remote Signal Cable.37 Installation with Conduit.
Contents MI 019-202 – February 2012 Calibration/Test Mode. 68 Calibration.69 Test.69 Error Messages.71 Operation Error Messages.71 Configuration Error Messages. Operation Via HART Communicator.73 Online Menu. 73 Explanation of Parameters. MI 019-202 – February 2012 Contents Appendix A.
Isolation Valves.107 Replacing the Sensor.107 Replacing or Installing an Isolation Valve.108 Style A Vortex Flowmeters.108 Style B Vortex Flowmeters, Single Isolation Valve.110 Style B Vortex Flowmeters, Dual Isolation Valve. Figures ANSI Flange Ratings; per ASME B16.5; Group 2.2 Materials; Standard Pressure Options: Style A: Cast Tubes (3/4 to 4 Inch, CF8M) and Flanges (CF8M, 4-inch Class 150 with Welded Slip-On Flanges) Style B: Cast Tubes (3/4 to 4 Inch, CF8M) and Welded Weld-Neck Flanges (316 SS).4 ANSI Flange Ratings. Loop Wiring 4 to 20 mA Output Flowmeters.41 Typical Multidrop Network.42 Wiring an 84F-T (Styles A and B) or 84W-T Flowmeter with a Pulse Output Transistor Switch (sinking) Counter Input with Receiver Supplied Power.43.

Figures MI 019-202 – February 2012 Bonnet Bolt Torquing Sequence.101 Sensor Replacement - Remotely Mounted Flowmeter.105 Bonnet Bolt Torquing Sequence.108 Single Isolation Valve (Style A).109 Dual Isolation Manifold (Style A).110 Bonnet Bolt Torquing Sequence. MI 019-202 – February 2012 Figures.
Tables Nominal Flow Velocity Limits.Electrical Safety Specifications.Configurable Parameters.Mounting Arrangements.Preparation of Remote Signal Cable (Junction Box End).Operation of Function Keys.Default Database When User Information Not Supplied.Default Database for Liquid.Default Database for Gas. MI 019-202 – February 2012 Tables. This signal is then conditioned by an Electronic Module and processed by the microcontroller to produce a digital signal, an analog (4-20 mA dc) signal, and in the 84F-T (Styles A and B) and 84W-T a pulse signal. 84F Style A Flanged and 84W Wafer Body Flowmeters PL 008-753 84F Style B Flanged Body Flowmeters Technical Information and Instructions B0800AJ Ensuring Premium Performance with Foxboro 84 Series Vortex Flowmeters MI 019-146 83 and 84 I/A Series Intelligent Vortex Flowmeter Universal Instruction Manual. Digital (HART): Digital signal conveyed at 1200 Baud transmission rates via Frequency Shift Keying (FSK) tones superimposed on power supply leads. Pulse Output in 84F-T (Styles A and B) and 84W-T only: Isolated 2 wire transistor switch.
Pulse rate (0 to 10, 100, or 1000 Hz) proportional to volumetric flow rate or total flow. MI 019-202 – February 2012 1. Introduction Maximum Working Pressure: 84F Flanged Body Flowmeters The maximum working pressure (MWP) of the flowtube at 100°F is shown on the data label. The MWP at other temperatures for the 84F Flanged Body Flowmeter without isolation valve is given in Figure 1 through Figure 12.
Introduction MI 019-202 – February 2012 Figure 2. ANSI Flange Ratings; per ASME B16.5; Group 2.2 Materials; High Pressure Options: Style B Only: Cast Tubes (3/4 to 4 Inch, CF8M) and Welded Weld-Neck Flanges (316 SS) 200 ° F 400 °. MI 019-202 – February 2012 1.
Introduction 200 ° F 400 ° F 800 ° F FLUOROLUBE SILICON EXTENDED SENSOR SENSOR TEMP. LIMIT LIMIT LIMIT (NO FILL) 1600 CLASS 600 1480 FABRICATED TUBES 1400 FLANGE MAT’L 6 TO 12 in: cs 1200 1000 CLASS 300. Introduction MI 019-202 – February 2012 Figure 6. ANSI Flange Ratings; per ASME B16.5; Group 2.8 Materials; Standard Pressure Options: Style B Only: Cast Tubes (3/4 to 12 Inch, CD3MN Duplex SS), and Welded Weld-Neck Flanges (ASTM A182 Gr. F51 Duplex SS) Figure 7. MI 019-202 – February 2012 1.
Introduction Figure 8. ANSI Flange Ratings; per ASME B16.5; Group 3.8 Materials; Standard Pressure Options: Style B Only: Cast Tubes (3/4 to 12 Inch, CX2MW Nickel Alloy equivalent to Hastelloy® C-22) and Welded Weld-Neck Flanges (N06022 equivalent to Hastelloy® C-22) Figure 9. Introduction MI 019-202 – February 2012 Figure 10. Metric Flange Ratings; per EN 1092-1; Material Group 14E0 Materials: Style A: Cast Tubes (DN15 to DN100, CF8M) and Flanges (CF8M, 4-inch Class 150 with Welded Slip-On Flanges) Style B: Cast Tubes (DN15 to DN100, CF8M) and Welded Weld-Neck Flanges (316 SS) Figure 11. MI 019-202 – February 2012 1.
Introduction Figure 12. Metric Flange Ratings; per EN 1092-1; Material Group 3E0: Style A: Fabricated Tubes, (DN150 to DN300, 304 SS) and Welded Weld-Neck Flanges (Carbon Steel) Style B: Cast Tubes (DN15 to DN300, CF8M) and Welded Weld-Neck Flanges (Carbon Steel) Figure 13. Introduction MI 019-202 – February 2012 Isolation Valves Flowmeters equipped with an isolation valve have Pressure-Temperature limits as shown in Figure 14.
The temperature range of your flowmeter is found within the model number on the data label as follows: 84F-T02S2KDTJK STD TEMP = D, F, R, or S TEMPERATURE RANGE. MI 019-202 – February 2012 1. Introduction 800 ° F 200 ° F 400 ° F FLUOROLUBE SILICON EXTENDED SENSOR SENSOR TEMP. LIMIT LIMIT LIMIT (NO FILL) 1600 P-T LIMITS 1440 EXTENDED TEMP.
WITH 1400 VALVE WITH ISOLATION GRAPHITE SEAT VALVE 1200 1000. Introduction MI 019-202 – February 2012 84W Wafer Body Flowmeters The maximum working pressure (MWP) of the flowtube at 100°F is shown on the data label.
The wafers are designed for a maximum Class 600 working pressure. Electrical Safety Specifications NOTE 1. MI 019-202 – February 2012 1. Introduction Table 2. Electrical Safety Specifications (Continued) Agency Certification, Electrical Types of Protection, Safety Design and Area Classification Application Conditions Code FM intrinsically safe for Class I, II, III, Connect per MI 019-177. 1, Groups A, B, C, D, E, F, G. Temperature Class T4.
Introduction MI 019-202 – February 2012 IECEx Compliance Documents IEC 60079-0:2011 Ed 6 IEC 60079-1:2007 Ed 6 IEC 600 Ed 6 IEC 600 Ed 2 IEC 600 Ed 1. MI 019-202 – February 2012 1. Introduction Configurable Parameters Table 3 lists all of the configurable parameters and the factory default for the 84 Vortex Flowmeter. Configurable Parameters Configurable with Parameter Factory Integral HART PC-Based Parameter Name Capability Default Indicator Comm. Introduction MI 019-202 – February 2012 Table 3. Configurable Parameters (Continued) Configurable with Parameter Factory Integral HART PC-Based Parameter Name Capability Default Indicator Comm. 4 EGU Pick list dependent on Mapping Output 2 Output Coms 3 Coms Poll Address 4PolAdr 0 through 15 Preambles.
MI 019-202 – February 2012 1. Introduction Table 3. Configurable Parameters (Continued) Configurable with Parameter Factory Integral HART PC-Based Parameter Name Capability Default Indicator Comm.
HART Message 32 characters maximum HART Message Flowtube 2NewTube Model Number 3 Model (16 characters 84F-T02 maximum) S1SSTJF. Installation Fundamental Installation Requirements These flowmeters must be installed by trained personnel to meet all applicable local installation regulations, such as hazardous location requirements, electrical wiring codes, and mechanical piping codes. The transmitter housing must be grounded to insure proper operation and peak performance. MI 019-202 – February 2012 2. Installation Electrical certification information is located on the right end of the data plate. The software version of your device can be found in View mode as 2 SW Rev Figure 15. Sample Flowmeter Data Plate Figure 16.
The installation guidelines given below are also summarized for your convenience in B0800AJ, Ensuring Premium Performance with Foxboro 84 Series Intelligent Vortex Flowmeters. Dimensions For overall dimensions of the flowmeter, refer to the appropriate dimensional print listed in “Reference Documents”. MI 019-202 – February 2012 2. Installation installations where this upstream requirement is not met, the type of disturbance must be selected from a picklist during configuration and the distance to the disturbance in pipe diameters entered. This assures that the flowmeter accuracy is maintained. Piping Alignment The bore of the pipe (flange) and flowmeter must be aligned (see “Mechanically Installing the Flowmeter Body”.
Installation MI 019-202 – February 2012 Liquid Installations For liquid flow installations, it is recommended that the meter be mounted upstream at least 5 pipe diameters from the control valve. In vertical installations, the meter should be mounted in the upward flowing leg. MI 019-202 – February 2012 2.
Installation On gas flow installations, avoid piping conditions that create standing pockets of liquids inside the meter. The best approach is to install the meter in a vertical line with flow in the upwards direction. Installation MI 019-202 – February 2012 SATURATED STEAM Figure 19. Piping for Saturated Steam Applications Superheated Steam When the process fluid is superheated steam, the electronics housing may be above or below the flowmeter body. The flowmeter should be insulated to maintain superheat conditions inside the flowmeter as well as insulating the electronics from heat.
MI 019-202 – February 2012 2. Installation Not Good Good Figure 21. Sensor Mounting to Minimize Effect of Vibration Ambient Temperature Limitations / Considerations The temperature limits of the electronics housing is -40 to +80°C (-40°F to +176°F). When installing the flowmeter, ambient temperature and proximity to other heat sources must be considered. Installation MI 019-202 – February 2012 Table 4.
Mounting Arrangements Flowmeter Orientation for Single (Shown) Saturated Superheated or Dual Measurement Flowmeter Liquid Steam Steam Housing below pipe Yes (4) Yes Yes (2) (3, 4, 6) Housing to side of pipe Yes (2) Housing to side and below Yes (6) Yes. MI 019-202 – February 2012 2. Installation Common practice is to install bypass piping so that the entire meter can be removed for servicing (see Figure 22). 5 PIPE 30 PIPE DIAMETERS DIAMETERS RECOMMENDED. RECOMMENDED SHUTOFF VALVES Figure 22. Typical Piping Configuration Location of Pressure and Temperature Taps For pressure and/or temperature compensated flow measurement applications, locate the pressure and temperature taps as follows. Installation MI 019-202 – February 2012 3.
On a steam installation, the pressure tap should be located on the top when the pressure measuring device (typically a pressure transmitter) is above the pipeline, and on the side when the measuring device is below the pipeline. MI 019-202 – February 2012 2. Installation GASKET GASKET FLOWMETER Figure 24. 84F Flowmeter Installation 3. Visually inspect for concentricity (centering and alignment) of mating flanges. Tighten bolts in accordance with conventional flange bolt tightening practice (that is, incremental and alternate tightening of bolts). Installation MI 019-202 – February 2012 NOTE If welding the flanges to the process piping is required, protect the flowmeter from weld splatter, which could affect flowmeter accuracy.
A solid sheet of gasketing should be installed at each end of the meter during welding. Remove this sheet and install the flange gaskets after welding.
MI 019-202 – February 2012 2. Installation 1/2 NPT or M20 conduit connections are provided on both the housing and the junction box. The remote electronics housing can be mounted to a vertical or horizontal DN 50 or 2-in pipe using the mounting bracket and U-bolt supplied.
Installation MI 019-202 – February 2012 COVER LOCK (2) (IF PRESENT) Figure 27. Cover Locks Positioning the Display The display (optional in some models) can be rotated within the housing to any of four positions at 90° increments. To do this, loosen the two captive screws, turn the display to the desired position, and retighten the screws. MI 019-202 – February 2012 2.

Installation JUMPER IN JUMPER IN PROTECT WRITE POSITION POSITION WRITE PROTECTION PINS Figure 28. Write Protect Jumper Positioning the Housing The flowmeter housing (topworks) can be rotated up to one full turn in the counterclockwise direction when viewed from above for optimum access to adjustments, display, or conduit connections. Installation MI 019-202 – February 2012 Electrical Installation This section describes procedures for installing wiring, conduit, and ground connections for both integral and remote mounted flowmeters and for preparing remote signal cables for interconnection. NOTE The transmitter housing must be grounded to insure proper operation and peak performance.
MI 019-202 – February 2012 2. Installation Table 5.
Preparation of Remote Signal Cable (Junction Box End) (Continued) 3. Insert the cable into the fitting until the cable is bottomed out inside the Fitting Compressed copper braid fitting.
Rotate the fitting one or two turns to pack the braid into place. Installation MI 019-202 – February 2012 Table 5. Preparation of Remote Signal Cable (Junction Box End) (Continued) 8. Cut an 1/2 inch long piece of shrink wrap and position it so that half the Knurled nut wrap covers the inner clear wrap- 1/2'.
MI 019-202 – February 2012 2. Installation Installation with Conduit The remote signal cable is shipped with the cable attached at both ends. To run the cable through conduit, the -T option must have been purchased.
This option facilitates a standard 1/2 NPT conduit connection at both the housing end and the flowmeter end. Accessing Field Terminals INTERNAL GROUND SCREW PULSE 4 TO 20 mA SIGNAL SIGNAL CONNECTIONS CONNECTIONS (84F-T AND 84W-T ONLY) – PHYSICAL EARTH GROUND REQ’D FOR EXPLOSIONPROOF (FLAMEPROOF) CERTIFICATIONS Figure 32. Identification of Field Terminals Wiring the Flowmeter to a Control Loop NOTE. MI 019-202 – February 2012 2. Installation component in the loop, excluding the flowmeter. The power supply must be capable of supplying 22 mA of loop current.
1400 1200 1000 MINIMUM LOAD 30 V MAXIMUM FOR WITH CONFIGURATOR INTRINSICALLY SAFE UNITS COMMUNICATOR 227.5 Ω. Installation MI 019-202 – February 2012 5. The flowmeter is equipped with an internal and external ground connection. Connect a ground wire to either terminal in accordance with local practice.
CAUTION If the loop is grounded, it is preferable to do so at the negative terminal of the dc power supply. Wiring a Flowmeter With a Pulse Output Two separate loops are required when using the pulse output on an 84F-T (Styles A and B) or 84W-T Flowmeter with the 4 to 20 mA or digital signal. Each loop requires its own power supply. (e) IF SHIELDED WIRE IS USED, TERMINATE THE SHIELD AT THE NEGATIVE TERMINAL OF THE RECEIVER. (f) REQUIRED FOR EXPLOSIONPROOF (FLAMEPROOF) APPLICATIONS.
Wiring an 84F-T (Styles A and B) or 84W-T Flowmeter with a Pulse Output Transistor Switch (sinking) Counter Input with Receiver Supplied Power. (e) MAXIMUM PULSE OUTPUT CURRENTIS 20 mA. LOAD RESISTOR MUST BE SIZED ACCORDINGLY. (f) REQUIRED FOR EXPLOSIONPROOF (FLAMEPROOF) APPLICATIONS. Wiring an 84F-T (Styles A and B) or 84W-T Flowmeter with a Pulse Output Transistor Switch (sinking) Counter Input with.
(e) MAXIMUM PULSE OUTPUT CURRENTIS 20 mA. LOAD RESISTOR MUST BE SIZED ACCORDINGLY. (f) REQUIRED FOR EXPLOSIONPROOF (FLAMEPROOF) APPLICATIONS. Wiring an 84F-T (Styles A and B) or 84W-T Flowmeter with a Pulse Output Transistor Switch (sourcing) Counter Input with. (e) THERE MUST BE AT LEAST 250 Ω TOTAL RESISTANCE BETWEEN THE PC-BASED CONFIGURATOR OR THE HART COMMUNICATOR AND THE POWER SUPPLY.
(f) REQUIRED FOR EXPLOSIONPROOF (FLAMEPROOF) APPLICATIONS. Wiring an 84F-T (Styles A and B) or 84W-T Flowmeter with a Pulse Output Using a 3-Wire Hookup. Operation Via Local Display Communication with the 84F-T (Styles A and B), 84F-U (Styles A and B), 84W-T, and 84W-U Vortex Flowmeters is carried out using the HART Communicator, a PC-Based configurator, or the optional Local Keypad/Display. General instructions for using the HART Communicator can be found in MAN 4250, HART Communicator Product Manual. MI 019-202 – February 2012 3.
Operation Via Local Display Table 6. Operation of Function Keys Function Left Arrow ( Moves left in the menu structure. Moves the cursor to the left in a data entry field. Escapes from changes in a picklist menu or data entry.
Answers No. Operation Via Local Display MI 019-202 – February 2012 To enter the password, use the Up/Down arrow keys to scroll through the list of acceptable characters. After selecting the desired character, press the Right arrow key to move to the next character. MI 019-202 – February 2012 3. Operation Via Local Display Configuration Database Each flowmeter is shipped from the factory with an operating configuration database. However, the flowmeter will not provide an accurate measurement if the configuration does not fit your application.
Operation Via Local Display MI 019-202 – February 2012 Table 9. Default Database for Gas (Continued) Parameter Metric English Flowing Density 9.546 kg/m 0.596 lb/ft Absolute Viscosity 0.0185 cP 0.0185 cP Upper Range Value Upper Range Limit for Upper Range Limit for Flowmeter Size Flowmeter Size.Liquid units of gallons, liters, imperial gallons, or barrels per unit time are not transferable.
MI 019-202 – February 2012 3. Operation Via Local Display can switch from one to another in sequence by using the Up/Down arrow keys. To enter the second level menu from a particular top level display, press the Right arrow key. To return to the top level from a second level menu item, press the Left arrow key. Operation Via Local Display MI 019-202 – February 2012 THIS IS THE NORMAL OPERATION MODE. IT Measurement DISPLAYS CONFIGURED MEASUREMENTS.
IT (Measurements) Values ALSO INDICATES IF DIAGNOSTIC CONDITIONS EXIST. THE SELECTED DEFAULT MEASURE- FOR DETAILS SEE MENT IS DISPLAYED WHEN THE TRANSMIT- “MEASURE MODE”. MI 019-202 – February 2012 3. Operation Via Local Display NOTE Certain parameters may be missing as you step through the menus described in this chapter depending on the configuration of your instrument. Measure Mode In normal operation, the flowmeter displays those measurements specified in Setup mode. If configured for cycle, you can cycle through the measurements manually by using the Manual. Operation Via Local Display MI 019-202 – February 2012 1 Status 2 MeaStat 3 Velcty 3 Raw Hz 3 KRef 3 KCor 3 KFlow Value 3 mA Out 3 Pulse Status 3 Reynld 2 WrProt 2 DiagEr 2 Reason Figure 42.
MI 019-202 – February 2012 3. Operation Via Local Display View Mode The View mode enables you to view the identity parameters. You can not edit them in this mode. To step through the list of the following parameters, use the Up and Down arrow keys. 1 View HART TAG 2 HrtTag.
Operation Via Local Display MI 019-202 – February 2012 If your transmitter is write protected, the display reads if you try to enter Setup mode. Rd Only In this case, you cannot enter Setup mode to make changes. You can, however, view but not edit the setup. MI 019-202 – February 2012 3.
Operation Via Local Display The following table lists the engineering units (EGUs) available. The available EGU options depend on the FlwMap selection (VolFlow, BVolFlow, MassFlow, or Velocity), and the actual EGUs are entered in the 1 Setup 2 Flow 3 FlwEGU menu. Operation Via Local Display MI 019-202 – February 2012 Table 12. All Flow EGU Descriptions (Volume, Mass, Base Volume, and Velocity) Description Description Description lb/ft3 pounds per cubic foot LTon/d long tons per day (2240 lbs) Sm3/m Standard cubic meters per minute lb/gal pounds per US gallon m3/s. MI 019-202 – February 2012 3. Operation Via Local Display Table 13. Viscosity, K-Factor, Density, and Temperature EGU Descriptions Description Description Viscosity Density PaSec Pa.s lb/ft3 pounds per cubic foot cPoise centipoise lb/gal pounds per US gallon K-Factor oz/in3 ounces per cubic in m3/p cubic meter per pulse kg/m3.
Operation Via Local Display MI 019-202 – February 2012 Setting Flow Parameters section of the Setup mode allows you to configure parameters for flow. 2 Flow, select, or 3 FlwMap VolFlow BVolFlow MassFlow Velocity NOTE Before changing the totalizer mappings from, the totalizer VolFlow BVolFlow. MI 019-202 – February 2012 3. Operation Via Local Display Setting Totals Parameters section of the Setup mode allows you to configure each of two totalizers. This is done 2 Total 3 TotNet 3 TotGrd NOTE Before changing the totalizer mappings from, the totalizer VolFlow BVolFlow.
Operation Via Local Display MI 019-202 – February 2012, configure the following: Total ♦, select, the pulse width as 0.5, 5, or 50 ms. 4 Pwidth ♦, select the units from the picklist provided. MI 019-202 – February 2012 3. Operation Via Local Display 1 EL PAR 1 EL PER FLOW DIRECTION FLOW DIRECTION DISTANCE DISTANCE FROM ELBOW FROM ELBOW 2 L0 PD PAR 2 L0 PD PER 2 L5 PD PAR 2 L5 PD PER FLOW DIRECTION SEPERATION. Operation Via Local Display MI 019-202 – February 2012 Setting Tag Parameters section of the Setup mode allows you to configure the following identification 2 Tags parameters: ♦, enter the device description. 3 HrtDes ♦, enter an alphanumeric description if desired.
3 HrtTag Setting Flowtube Parameters section of the Setup mode allows you to configure the following flowtube. MI 019-202 – February 2012 3. Operation Via Local Display Setup Menu Tree 1 Setup 3 New- 2 Fluid ∇ Edit 3 FldTyp (Read Only) 3 Name 3 TmpEGU 3 FlwTmp 3 DenEGU. 3 FlwDen 3 BasDen (Read Only) 3 LfciEGU (Read Only) 3 Lfci 3 VisEGU. Operation Via Local Display MI 019-202 – February 2012 3 TotNet 2 Total 4 Map 4 EGU. 3 TotGrd 4 Map 4 EGU. 4PolAdr 3 Coms 2 Output 4Preambl 3 Pulse 4 Pulse If Raw Pul=Raw If Rate 4 Freq 4 “Tot P/U”.
MI 019-202 – February 2012 3. Operation Via Local Display 3 HrtDes 2 Tags 3 HrtTag 3 Model 2NewTube 3 Special 3 Special 4 TubDia 3 Ref No 4 TubAlp 4 LfUFac 3 K Ref 4 K EGU 4 K Ref 4 LoPwd 2Passwd 4 HiPwd. Operation Via Local Display MI 019-202 – February 2012 Calibration, go to to have the flowmeter automatically set the Low Flow Cut-In. In 2 Calib 3 SetLFCI doing this, the flowmeter chooses the lowest level at which no signal is detected over a 20-second time interval.
MI 019-202 – February 2012 3. Operation Via Local Display 2 Calib 3 CalLFCI 1 Cal/Tst 3 Cal mA 4 Restore 4 Cal4mA 4Cal20mA 4CalDate 2 Test 3 Set Dig 4Initial 3 Set mA 3 Set Hz SelfTst Figure 48. Operation Via Local Display MI 019-202 – February 2012 Error Messages Operation Error Messages This section defines error messages that may be displayed and actions that can be taken to correct the error. Some messages appear periodically while seeing a valid flow measurement.
This typically occurs when ‘soft’. MI 019-202 – February 2012 3. Operation Via Local Display Table 15. Configuration Error Messages (Continued) Message Explanation Corrective Action No Pulse An incorrect model code has been entered. Enter the correct model code which Hardware The model code entered was for a flowmeter begins with 84F-E, 84W-E, 84F-U with a pulse output.
Operation Via HART Communicator Online Menu 1. Device Setup 1. Process Variables 1. Diag/Service 2. Basic Setup 3. Detailed Setup (SV) 4. MI 019-202 – February 2012 4.
Operation Via HART Communicator 1. Pulse Operations 1. Process Variables 1. Net Total Value 2. PV Configuration 2. Net Operations 3.
Foxboro Pressure Transmitter Idp10
Total Units 3. Grand Total Value 4. Operation Via HART Communicator MI 019-202 – February 2012 1.
Set Fluid Defaults.If Density Units = Custom, specify 2. Fluid Name Custom Dens Label 3. Temperature Units Custom Dens Offset 4. Process Temp Custom Dens Slope 5.
Density Units. 6.
MI 019-202 – February 2012 4. Operation Via HART Communicator Model Code Serial Number K Factor PV USL Fluid Name Fluid Type PV Min Span Temperature Units LFCI LFCI Index Process Temperature Density Units PV Units Process Density Net Total Units Base Density Grand Total Units Abs Viscosity Units. Operation Via HART Communicator MI 019-202 – February 2012 Explanation of Parameters NOTE The fast-key path shown is based on a frequently used configuration.
If certain parameters are configured off or infrequently used parameters configured on, the fast-key path may be different. Parameter Fast-Key Path Explanation. MI 019-202 – February 2012 4. Operation Via HART Communicator Parameter Fast-Key Path Explanation Date 1,2,5,3 In Diag/Service, enter the date of the last calibration. 1,4,5,5 In Detailed Setup, enter the date of the last calibration.
1,4,4,2,5,3 In Review, shows the last calibration date. Density Units 1,4,1,4,5 In Detailed Setup, select the density unit from the picklist. Operation Via HART Communicator MI 019-202 – February 2012 Parameter Fast-Key Path Explanation K Factor 1,2,6,3 In Diag/Service, shows the K-Factor value. 1,3,4 In Basic Setup, enter the K-Factor. 1,4,2,3 In Detailed Setup, enter the K-Factor. In Review, shows the K-Factor. K Factor Units 1,3,3 In Basic Setup, path to selecting the K-Factor unit.
MI 019-202 – February 2012 4. Operation Via HART Communicator Parameter Fast-Key Path Explanation Output Configuration 1,4,4 Path to configuring the output parameters. P/CuFt 1,3,3,2 Sets the K-Factor unit to pulses per cubic foot. 1,3,3,1 Sets the K-Factor unit to pulses per liter. Piping 1,4,1,5 Path to configuring the piping parameters.
Operation Via HART Communicator MI 019-202 – February 2012 Parameter Fast-Key Path Explanation Pulse Output 1,4,4,3 Path to configuring the pulse output. Pulse Resolution 1,4,4,3,5 Enter the units per pulse. Pulse Status 1,2,6,9 Shows the pulse status.
Pulse Total EGU 1,4,4,3,4 Select the unit from the picklist provided. MI 019-202 – February 2012 4. Operation Via HART Communicator Parameter Fast-Key Path Explanation Set Fluid Defaults 1,3,2 Path to setting the default parameters for the type of fluid 1,4,1,4,1 selected (liquid, gas, or steam).
Set Pulse Out 1,2,4,3 Procedure to set the pulse output to 0 Hz, the maximum 1,4,4,3,6 frequency, or another value. Troubleshooting CAUTION Components in your flowmeter are ESD sensitive and thus are susceptible to damage resulting from electrostatic discharge.
Invensys recommends that you be grounded via a conductive wrist strap or by standing on an ESD mat when performing maintenance in the electronics compartment or the remote junction box, and if the housing is removed. MI 019-202 – February 2012 5. Troubleshooting 2.
If the LFCI is higher than desired, there are several possible causes: a. Check the flowmeter sizing. The flowmeter could be over-sized for the application, resulting in the need to provide a measurement at a very low flow ™. Troubleshooting MI 019-202 – February 2012 2.
Check the flowmeter status to see it has not “failed low”. The flowmeter is configurable to fail either “low” or “high”. The mA value in the fail-low mode is 3.6 mA. (The mA value in the fail-high mode is 22 mA.) 3.
MI 019-202 – February 2012 5. Troubleshooting 6.
Check the pre-amplifier: a. Disconnect the sensor leads b. For a standard temperature sensor, connect a 2200 pF +/- 5% 50V NPO ceramic capacitor to the + (brown) terminal of the sensor terminal block. Troubleshooting MI 019-202 – February 2012 5.
Check the inside for broken or pinched wires and/or connectors that are not engaged. Check the voltage level at the cable end of the blue and red wires. The voltage should be the same as was measured on the field terminals.
MI 019-202 – February 2012 5. Troubleshooting c. Verify the URV is correctly configured. Incorrect pulse output value.
Check the configuration of the pulse output to verify that it is correct. ♦ Raw Pulse: the raw vortex shedding frequency. Introduction The operation of the 84F-T (Styles A and B), 84F-U (Styles A and B), 84W-T, and 84W-U Vortex Flowmeters consists of three basic functions: (1) generation and shedding of vortices in the fluid stream, (2) sensing of vortices, and (3), amplification, conditioning, and processing of the signal from the vortex sensor. MI 019-202 – February 2012 6. Maintenance The Extended Temperature Range sensor consists of two piezoelectric crystals sealed inside a capsule having two process diaphragms, on opposing sides, connected internally by a mechanical shuttle. The vortex shedding process creates an alternating differential pressure across the capsule that is transmitted via the diaphragm-shuttle mechanism to the crystals.
Maintenance MI 019-202 – February 2012 4. Unscrew the two captive screws, one on each side of the electronic module. Pull the electronic module out of the housing far enough to be able to disconnect the wires from the terminal blocks on the back of the electronic module. MI 019-202 – February 2012 6. Maintenance 5.
Turning the electronic module one turn maximum to take up the slack in the wires, locate the module in the housing over the two mounting holes. Making sure that no wires are pinched under the module, tighten the captive mounting screws. Maintenance MI 019-202 – February 2012 Removal Procedure WARNING Before proceeding, ensure that power is removed from the flowmeter. Remove the electronic module. See “Electronic Module Removal” on page 90. If your flowmeter has explosionproof/flameproof electrical certification, disconnect the two wires from the PE ground screw in the electronics housing. MI 019-202 – February 2012 6.
Maintenance HOUSING GROUND ANTI-ROTATION SCREW SCREW OR RETENTION CLIP ELECTRONICS CABLE BARRIER ELECTRONICS CABLE NECK BOARD PE WIRE SENSOR WIRES O-RING NECK SENSOR WIRES Figure 55. Preamplifier Assembly - Integrally Mounted Installation Procedure WARNING Before proceeding, ensure that power is removed from the flowmeter.
Maintenance MI 019-202 – February 2012 1. Remove the neck board. See “Removal Procedure” on page 93. Feed the (2 or 4) wires from the cup through the hole in the center of the neck board and connect them to the 4-position terminal block on the board. MI 019-202 – February 2012 6. Maintenance eamplifier Replacement With integrally mounted electronics, the preamplifier is located on the neck board.
See “Neck Board Replacement” on page 92. With remotely mounted electronics, use the following procedure referring to Figure 56. Aircraft landing games. Removal Procedure WARNING Before proceeding, ensure that power is removed from the flowmeter. Maintenance MI 019-202 – February 2012 Installation Procedure WARNING Before proceeding, ensure that power is removed from the flowmeter. NOTE The replacement preamplifier is shipped in a protective antistatic plastic bag. Do not remove the preamplifier from this bag until it is ready to be installed in a flowmeter.
MI 019-202 – February 2012 6. Maintenance Sensor Replacement The flowmeter does not need to be removed from the pipeline for sensor replacement. The pipeline must, however, be shut down and emptied before loosening the bonnet bolts. Replacing the sensor does not cause a shift in the K-factor.
Therefore, the flowmeter does not require recalibration. Maintenance MI 019-202 – February 2012 Sensor Assembly Installation NOTE Before beginning the assembly procedure, verify that you have the correct kit of parts. Kit part numbers can be found in PL 008-714 for Style A and PL 008-753 for Style B. MI 019-202 – February 2012 6.
Maintenance HOUSING GROUND SCREW ANTI-ROTATION SCREW OR RETENTION CLIP BARRIER ELECTRONICS CABLE NECK BOARD CUP O-RING PE WIRE SENSOR WIRES BONNET O-RING SENSOR ASSEMBLY GASKET FLOW DAM Figure 58. Sensor Replacement - Integrally Mounted Flowmeter.
Maintenance MI 019-202 – February 2012 WARNING It is important that the gasket be sealed uniformly to provide a good seal. The following two steps assure a uniform seal. Failure to follow these steps could result in personal injury due to gasket leakage. MI 019-202 – February 2012 6. Maintenance 14. If your housing has a retention clip, insert the clip over the boss in the housing neck so that the hole in the clip is aligned with the hole in the boss.
Install the screw but do not tighten. Maintenance MI 019-202 – February 2012 Table 17. Maximum Test Pressure Test Pressure Duplex SS, Nickel alloy CX2MW (equivalent to Hastelloy ® C-22 316 SS (1.5X Carbon Steel Model End Connection MWP) (1.5X MWP) (MWP) ANSI Class 150 413 psi 435 psi 428 psi ANSI Class 300. MI 019-202 – February 2012 6. Maintenance Sensor Assembly Installation NOTE Before beginning the replacement procedure, verify that you have the correct kit of parts. Kit part numbers can be found in PL 008-714 for Style A and PL 008-753 for Style B.
Maintenance MI 019-202 – February 2012 WARNING Style A bolts cannot be used for Style B Vortex meters. Check the corresponding Parts List document, and contact Invensys with any questions. Do not use the bonnet bolts in the sensor replacement kits for 84F-xxxxxL flowmeters (dual measurement with isolation valves). MI 019-202 – February 2012 6. Maintenance 8.
Continue to tighten as follows: a. For Model 84 Style A flowmeter, continue to tighten in steps of 7 N m (5 lb. using the same sequence. The maximum torque needed for safe operation is 34 m (25 lb ft). Appendix A. Isolation Valves Isolation valving is available in single and dual measurement versions for standard and extended range sensors.
The following procedure applies to all versions. Replacing the sensor in this type of unit is essentially the same as replacing a sensor in units without isolation valving. However, particular care must be taken since the process does not need to be shut down. MI 019-202 – February 2012 Appendix A. Isolation Valves Replacing or Installing an Isolation Valve Style A Vortex Flowmeters The flowmeter does not need to be removed from the pipeline to replace the isolation valve. However, the pipeline must be shut down and emptied before loosening the mounting bolts.
Appendix A. Isolation Valves MI 019-202 – February 2012 BONNET O-RING SENSOR GASKET FLOW DAM ISOLATION VALVE OPEN WRENCH FLAT CLOSE GASKET FLOW DAM Figure 62. Single Isolation Valve (Style A). MI 019-202 – February 2012 Appendix A. Isolation Valves O-RING BONNET SENSOR FLOW DAM GASKET DUAL ISOLATION MANIFOLD FLOW DAM GASKET Figure 63. Dual Isolation Manifold (Style A) Style B Vortex Flowmeters, Single Isolation Valve The flowmeter does not need to be removed from the pipeline to replace the isolation valve. However, the pipeline must be shut down and emptied before loosening the mounting bolts.
Appendix A. Isolation Valves MI 019-202 – February 2012 WARNING It is important that the gasket be sealed uniformly to provide a good seal. The following two steps assure a uniform seal. Failure to follow these steps could result in personal injury due to gasket leakage.
MI 019-202 – February 2012 Appendix A. Isolation Valves BONNET O-RING SENSOR GASKET FLOW DAM ISOLATION VALVE WRENCH FLAT GASKET FLOW DAM ADAPTER PLATE Figure 65.
Single Isolation Valve (Style B). Appendix A.
Isolation Valves MI 019-202 – February 2012 Style B Vortex Flowmeters, Dual Isolation Valve The flowmeter does not need to be removed from the pipeline to replace the isolation valve. However, the pipeline must be shut down and emptied before loosening the mounting bolts. MI 019-202 – February 2012 Appendix A.
Isolation Valves WARNING It is important that the gasket be sealed uniformly to provide a good seal. Failure to follow these steps could result in personal injury due to gasket leakage. Reconnect the conduit and external wiring. Refer to “Electrical Installation” on page 35. Index Calibration/Test Mode 68 Configuration Database 50 Cover Locks 32 Database, Configuration 50 Dielectric Test 97 Dimensions 21 Display, Positioning the 33 Electrical Safety Specifications 13 Electronic Module 90 Removal 90 Replacement 91 Error Messages 71 Flow Parameter, Setting 61 Flowtube Parameters, Setting 65 Fluid Parameters, Setting 57 Housing, Positioning the 34.
MI 019-202 – February 2012 Index Maintenance 89 Measure Mode 54 Menu Tree, Setup 66 Menu Tree, Using the 51 Mounting the Remote Electronics Housing 31 Neck Board Replacement 92 Operation via Local Display 47 Output Parameters, Setting 62 Password 48 Piping 21 Effects of Piping on Flowmeter Performance 21 Gas Installations 23. Index MI 019-202 – February 2012 Unpacking 19 View Mode 56 Wiring Field Termination 38 For 4 to 20 mA Output 39 For Pulse Output 42 Write Protect Jumper, Setting the 33. JAN 2010 Vertical lines to the right of text or illustrations indicate areas changed at last issue date. Invensys Operations Management Invensys, Foxboro, and I/A Series are trademarks of 5601 Granite Parkway Suite 1000 Invensys plc, its subsidiaries, and affiliates.